自動車産業
当社がパートナー企業とともに開発したソリューションは、熱可塑性樹脂に関する数十年にわたる知識と経験に基づいています。
多くのメーカーは、コンベヤシステムが所有コストにおける経済的負担となることを理解しています。
頻繁なベルト交換、それに伴う高額なダウンタイム、増加する保守コスト、さらに外部業者の現場作業が困難になる状況など、さまざまな課題が発生しています。
これらの課題を解決するために、より経済的で効率的な搬送ソリューションを提供することが重要です。
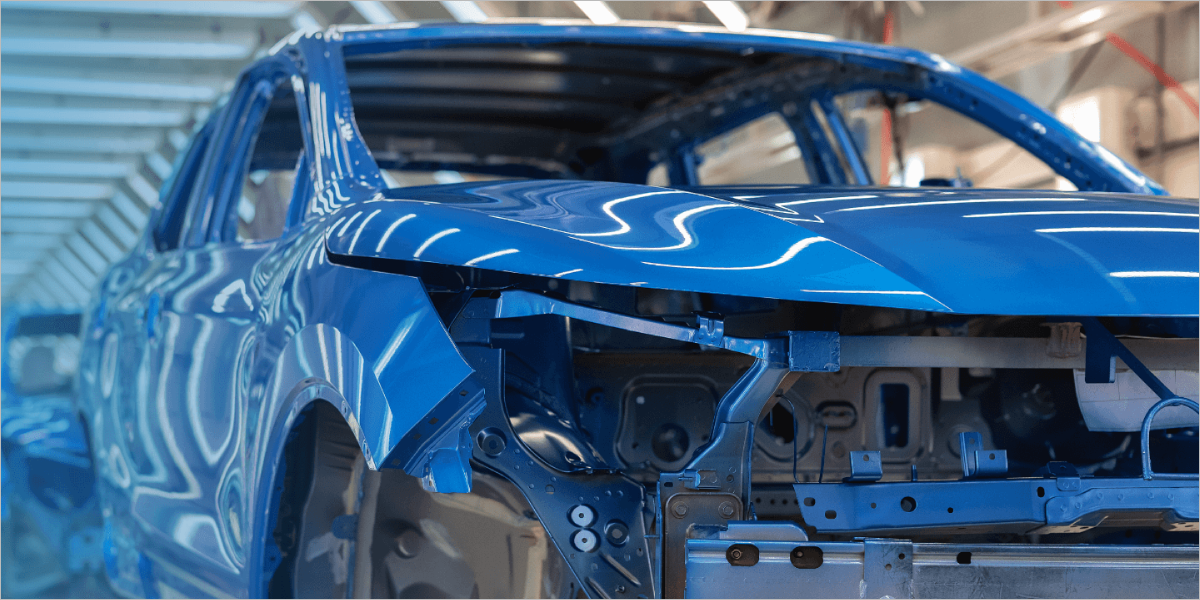
自動化組立工場
ボルタは、自動車の車体を組立ラインで連続的に搬送するための狭幅のベルトを開発するという課題に取り組みました。
このベルトは、軸間25メートル、幅55mmのシステム向けに設計され、4トンを超える荷重を運搬することが可能です。さらに、幅広のベルトを使用すれば、より重い荷重の搬送にも対応できます。
このベルトは伸びることがなく、継ぎ目もありません。また、耐摩耗性と耐塗装性に優れており、長時間のダウンタイムが許されない工業環境に最適です。
従来型のベルトでは、交換の際に組み立て途中の車両を一時的にラインから取り外す必要がありました。そのため、ベルト交換後に車両を再配置する作業が発生し、生産のダウンタイムがさらに延びるという課題がありました。ボルタベルトの導入により、これらの問題を解決しました。
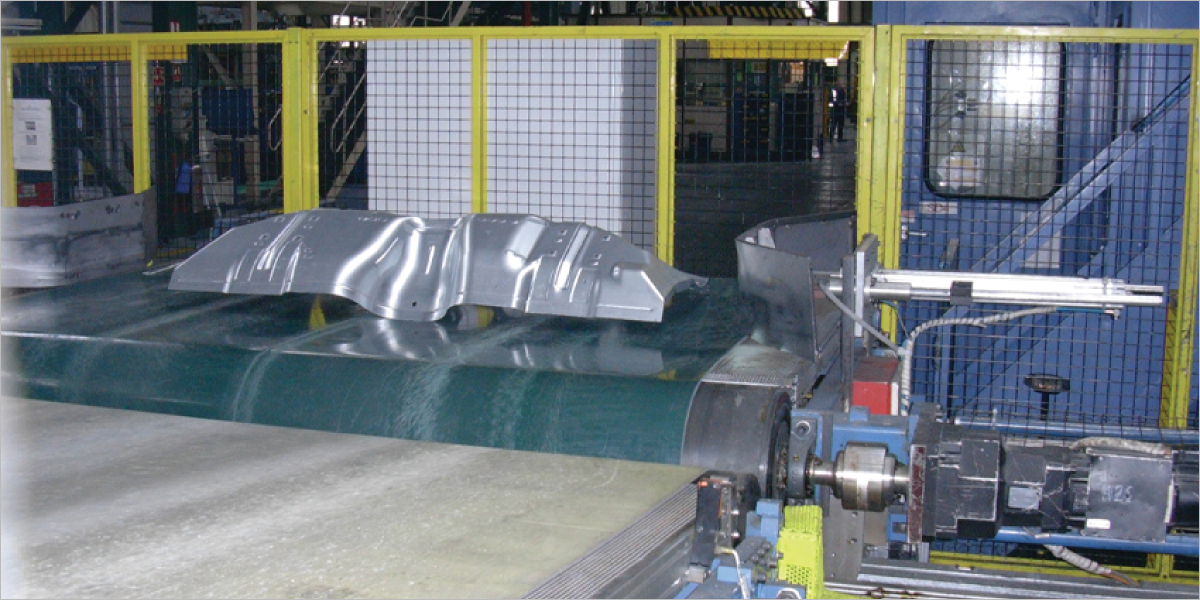
プレス加工ライン
国際的な大手自動車メーカーのプレス加工室では、生産管理にカイゼンシステムを採用し、車のドアをプレス加工するコンベヤの生産性向上に取り組みました。
この工場では、2分ごとに1台の車がラインを流れるため、従来の3層ファブリックベルトが6~8か月ごとに破損することは大きな負担となっていました。
そこで、ボルタは3mm厚の熱可塑性ベルトを提供しました。この幅1600mmの長尺コンベヤへの設置において、ボルタのFBW溶着ツールを使用したことで、初回の施工時間を4時間短縮できました。しかし、1か月後にオペレーターの操作ミスにより、ドアパネルがベルト中央部を切断する事故が発生しました。工場長は、従来の布製ベルトの経験から「ベルトは廃棄するしかない」と考えていました。しかし、ボルタの現地チームがすぐに出動し、溶着技術を用いて補修しました。この修復はほぼ目に見えないほど完璧で、その後ベルトはさらに2年半使用可能となりました。この結果、3回分のベルト交換を回避し、約2万ドルの生産停止コストを削減することができました。
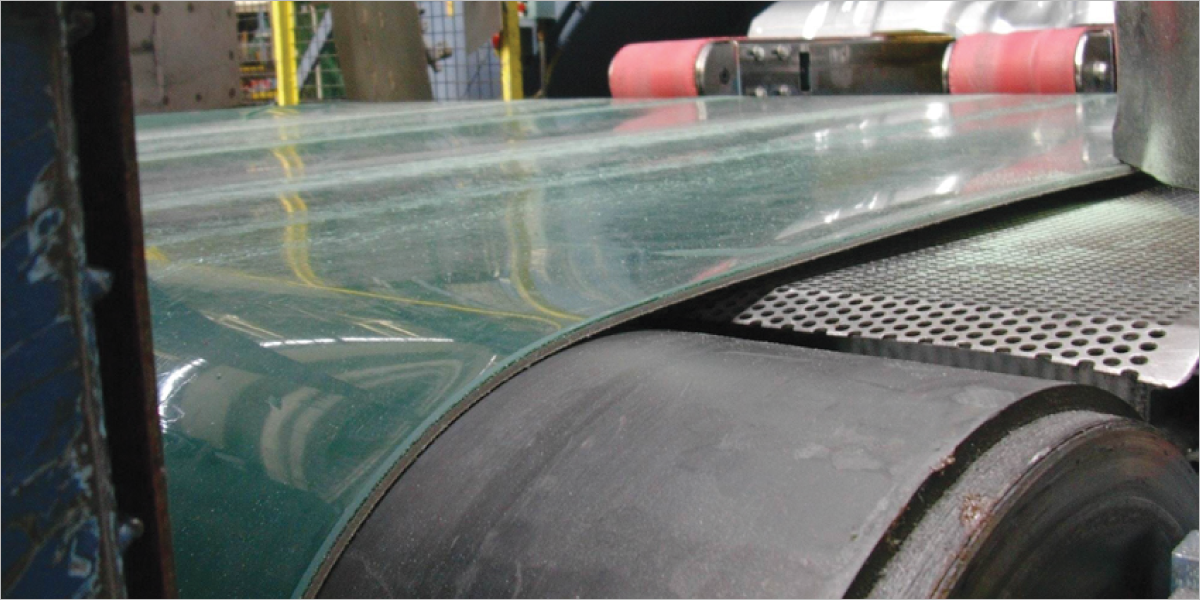
塗装室
自動車の塗装室は完全な無塵環境である必要があります。微細な粒子が車体に付着すると、塗装品質に影響を及ぼすため、メーカーは埃や繊維、その他の粒子を発生させる材料の使用を極力避ける必要があります。
塗装室では、車体を塗装ブースへ出し入れする際にコンベヤが使用されます。この工程はタイヤが装着される前に行われるため、車体を直接搬送するシステムが求められます。
ボルタの特殊な熱可塑性ベルトは、車体のフレームに傷をつけるリスクがなく、繊維の剥離も発生しないため、塗装室向けの搬送システムとして採用されました。
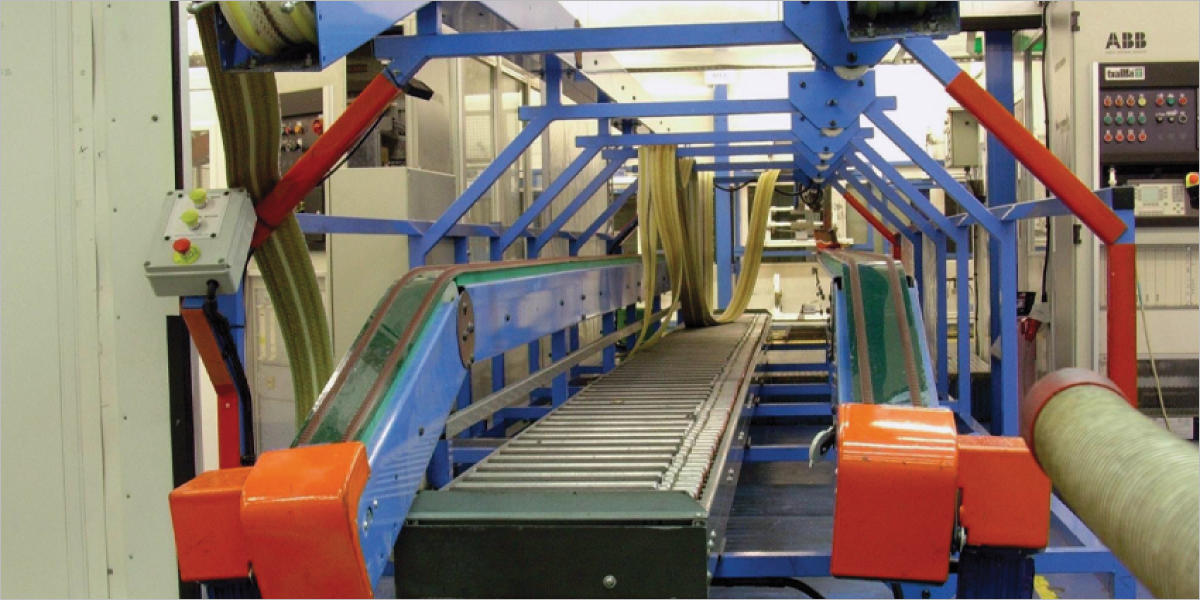